Navigating critical challenges and tapping into reshoring opportunities
Manufacturing, as a sector is grappling with many challenges.
Disruptions in supply chains triggered by the pandemic, have been followed by persistent shortages of raw materials and vital components, alongside a notable spike in energy costs.
Geopolitical disruption, such as the conflicts in Ukraine and the Gaza Strip, coupled with tensions in the Suez Canal, are driving up shipping rates, further complicating global trade dynamics.
Achieving Green Transition in a competitive and sustainable fashion remains an urgent imperative while, the increasing shortage in both skilled and unskilled labor, adds further layers of complexity that need to be addressed.
Additionally, rapidly evolving consumer preferences and expectations heighten the necessity for flexibility and adaptability among manufacturing enterprises, that will enable them to navigate unforeseen shifts in demand.
Reshoring was prompted by the need of numerous businesses to reassess the widespread practice of relocating production lines to low-cost, developing markets, in light of new emerging risks. These include supply chain disruptions, rising transportation costs, slow and uncertain deliveries, and heightened exposure to the consequences of conflicts and natural disasters, in addition to nascent trade conflicts.
The emerging trend of reshoring manufacturing activities closer to domestic markets or neighboring countries, represents a notable opportunity for Greek manufacturing.
Moreover, the reshoring trend is intertwined with the urgent need to address the issue of the EU's strategic dependence, particularly concerning critical raw materials, metals, and minerals. Production or extraction of these materials currently occurs in emerging markets, underlining the necessity for strategic diversification for resilience within the EU manufacturing landscape.
Three critical challenges for the Greek manufacturing sector
In order for the Greek manufacturing sector to grow and thrive in this changing environment, three critical challenges should be tackled:
Ι. Invest in manufacturing excellence, which entails striving for high-quality production by optimizing processes, technologies, and human capabilities.
ΙΙ. Promote digital transformation for the transition toward the factory of the future.
ΙΙΙ. Adopt a sustainability model that generates long-term value for businesses, the environment, and society as a whole.
All three of these challenges are closely tied to the imperative of further developing the knowledge and skills of the workforce.
The Greek manufacturing enterprises’ perspective
The study examines what motivates manufacturing businesses to address such challenges, as well as the anticipated benefits, the obstacles they need to overcome, and the key success factors.
The importance of having a clear vision and measurable goals, the pivotal role of the leadership in fostering a culture that embraces and effectively manages change, and the critical need for training and developing talent, are also analyzed. Additionally, the study underlines that manufacturing excellence, digital transformation, and sustainability initiatives, should not be piecemeal, but integrated into a comprehensive manufacturing development strategy.
Regarding the future of the sector over the next three years
58%are optimistic or extremely optimistic.
However, although 46% of respondents say that reshoring will positively affect the overall growth of Greek industry, only 28% say the same about their own organization.
Among survey respondents,
46%believe that reshoring presents an opportunity for the growth of the Greek economy.
However, only
28%perceive reshoring as an opportunity for their organization's growth.
The most significant external challenges of the past three years, include energy and fuel cost (72%), human capital (65%), supply chain disruptions (63%), and raw and packaging materials cost (61%). For the next three years, human capital (73%) was mentioned as a top challenge. Specifically, businesses are concerned both about accessing skilled human capital with specialized expertise and knowledge (85%), as well as unskilled or entry-level human capital with basic skills and qualifications (62%).
Key external challenges encountered
over the last three years:
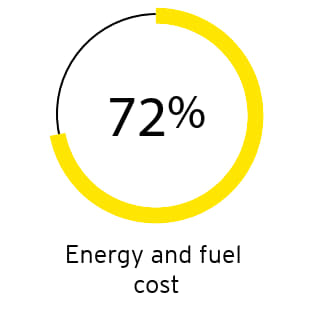
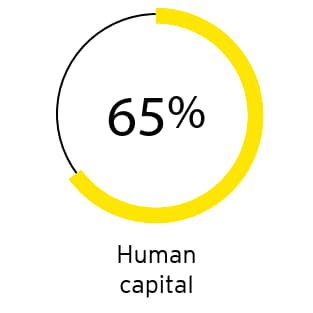
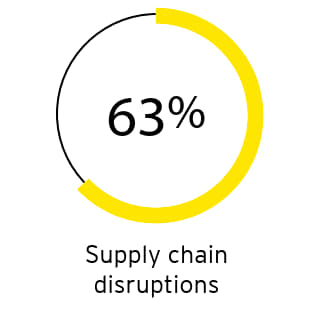
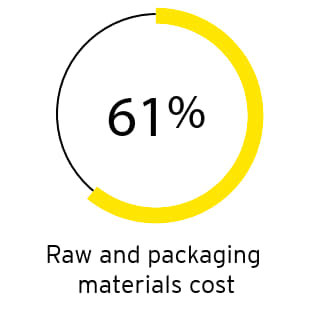
Over the next
three years:
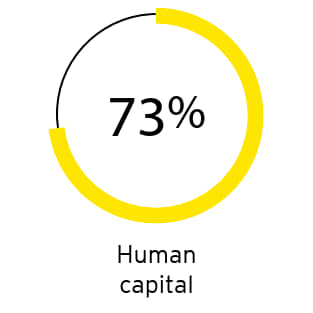
The vast majority of survey participants state that their businesses have implemented manufacturing excellence (81%), digital transformation (87%), and sustainability (87%) initiatives in their manufacturing activities. However, in all three cases, data shows that most businesses implement such actions on an ad hoc basis – where they deem necessary – or on a small scale, or within specific operational units, rather than as part of a structured program or broader strategy.
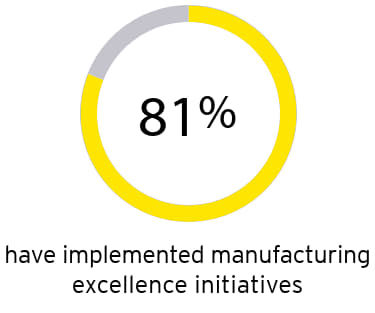
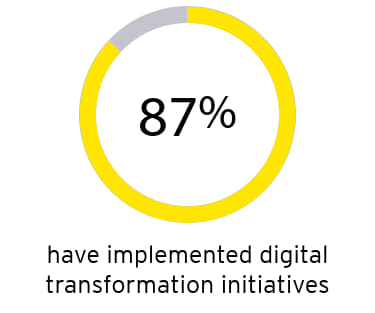
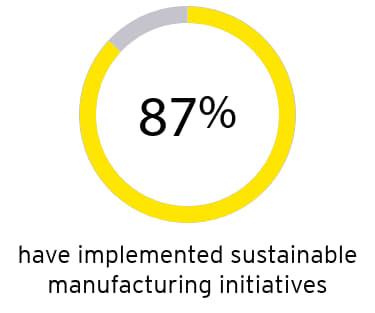
Specifically with regard to manufacturing excellence, respondents rate the level of success of the initiatives implemented so far as satisfactory (67%), high (20%), or very high (2%). Most actions undertaken concern functional areas of production (90%) and quality (69%), while top management commitment and support (76%), and high employee engagement (57%), are cited as the most significant factors for the successful implementation of such initiatives.
Critical factors for driving the successful implementation of manufacturing excellence initiatives:
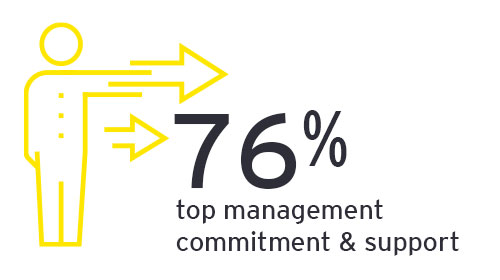
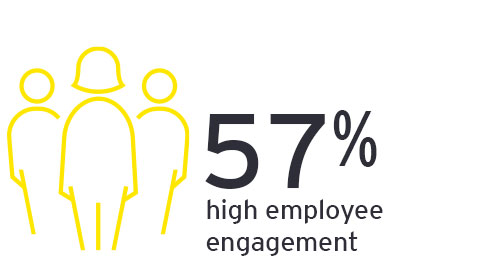
As for digital transformation initiatives, respondents believe that the most significant objectives achieved, include increased labor productivity (43%) and improved operational efficiency (41%). Digital technologies or systems already integrated or being integrated today, mainly include Warehouse Management Systems (WMS - 62%), MES/MOM/real-time production data (47%), and predictive maintenance analysis (41%). For the next three years, the top priorities identified are predictive maintenance analysis (45%), as well as artificial intelligence (AI) and data analytics (43%).
Main objectives achieved by the implementation of digital transformation initiatives:
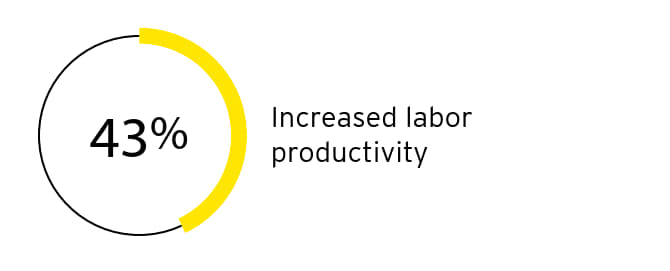
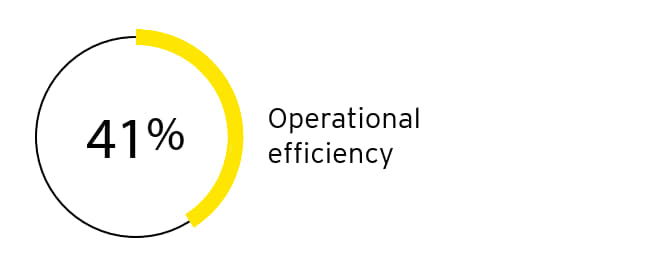
Businesses seem to have recognized the growing need for the use of AI, as 83% plan to implement AI-based solutions. Over the next three years, businesses plan to leverage AI particularly in production planning and scheduling (46%), quality control (43%), predictive maintenance (38%), inventory management (37%), and supply chain optimization (36%).
Finally, regarding cybersecurity, one out of four respondents (23%) reported that their organizations have strong cybersecurity infrastructure and processes in place, while 43% stated that significant initiatives have been implemented to safeguard operations.
According to the research findings,
83%intend to adopt AI-based solutions.
Regarding cybersecurity,
23%stated that their organizations have strong cybersecurity infrastructure and processes.
Lastly, with regard to sustainability initiatives, the most significant goals achieved were the reduction of the environmental footprint (68%), as well as energy efficiency (60%), and compliance with existing and upcoming ESG regulations and sustainability reporting (57%). Main areas where significant actions have already been implemented, include waste management and the circular economy (87%), as well as energy efficiency and renewable energy sources (79%).
Main areas where actions related to sustainability have been implemented:
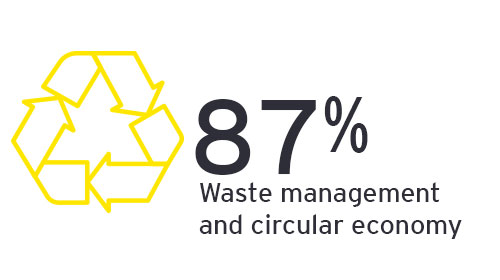
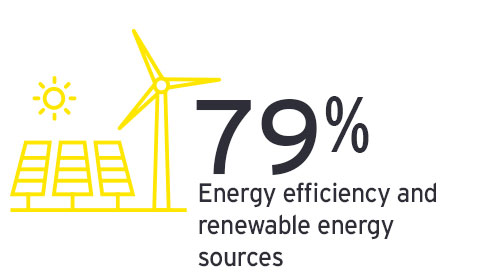
Summary
The recent study conducted by EY Greece, in collaboration with SEV - Hellenic Federation of Enterprises, analyzes the next day of the Greek manufacturing sector. The study features the views of 112 representatives of manufacturing enterprises in Greece, on three key pillars: manufacturing excellence, digital transformation, and sustainability.